This 3-part blog series was inspired by a live presentation delivered at SEMICON India on September 11, 2024
Live Presentation
“Evolution of Smart Manufacturing: Lessons for India’s Leap Ahead to Advanced Automation.”
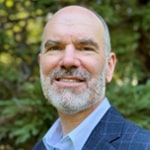
Scott Rothenberg
India can skip over the decades and billions of dollars that its peers invested to develop the cutting-edge smart manufacturing technologies that are best practice today. In doing so, new semiconductor factories in India, both wafer fab and packaging, can enjoy improved time to market while optimizing yield, cost, and output. In short, India’s semiconductor industry can benefit from the collective work, investment and learnings of the rest of the world to build the smartest, most productive factories, building the highest quality products at the lowest cost. They can shift the S-curve, as we say, to produce more good die at every stage of the factory lifecycle.
In this first blog, we’ll look at the origins of manufacturing and what it means to make it “smart.”
Early manufacturing
The English word, “manufacturing” comes from the words, “hand” and “made,” and it’s not a new practice. In fact, archaeologists have determined that the first manufactured products date back more than 2.5 million years. Evidence shows that India has had manufacturing for nearly half that time. An Acheulean stone axe manufactured more than one million years ago was found in Isampur, India.
To manufacture the stone axe, someone had to first recognize a need and envision a solution to address it; create a design; specify the raw materials; build specialized process equipment; execute complex manufacturing steps flawlessly and test the final product to ensure it met requirements. These basics of manufacturing have not changed, but how all of this is carried out is vastly different.
Stone to steam
Over the million years since the axe was made, the Stone Age gave way to the Bronze Age, which led to the Iron Age and eventually, the Industrial Age with steam-powered looms and mills. One hundred years later, after the discovery of electricity, assembly lines and powerful new machines were invented to revolutionize manufacturing. Industry 2.0 was born. It was about 100 years until the development of electronics and computers in the late 1960s ushered in Industry 3.0. Just 50 years later, the semiconductor industry pioneered the technologies that led to Industry 4.0.
Buzzwords vs. blueprints
Engineers like to build flowcharts and schematics, and there are countless versions available on the Internet that illustrate a hypothetical Industry 4.0 solution. You’ll see elements that include components like digital twins, big data, cloud, and Internet of Things to capture data from sensors, and 5G to move it around. While these illustrations are interesting, they are not entirely helpful for someone actually ready to build their own smart factory with limited time, resources and budget.
Focus on the goal
At this point in the discussion of how to build a smart factory, we advise customers to step back and think about what they’re really trying to achieve. Despite the numerous buzzwords and non-stop emerging technologies, the goals remain clear: produce better die faster and at a lower cost; achieve higher productivity and fewer defects. Never lose sight of these objectives.