Interview
Bing Wang, Director of CIM Solution, discusses how to achieve critical factory KPIs with an industry-proven turnkey solution: Applied Smartfactory® CIM solution.
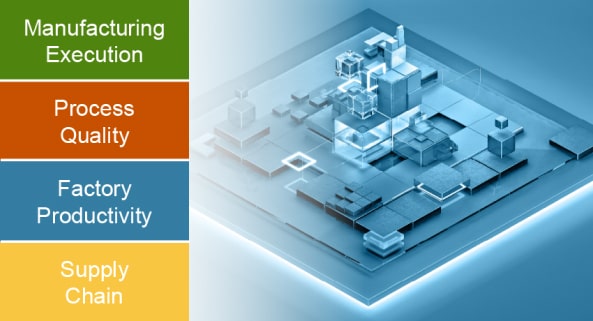
Our Insights blogger sat down with Bing Wang to find out how a turnkey CIM solution can accelerate a semiconductor fab’s yield and product output, and at the same time reduce cycle time and costs. What’s the recipe for successfully deploying such a turnkey solution?
Insights: First, in the context of semiconductor, how would you define “computer integrated manufacturing”?
Bing: It’s simply the approach of using computer software applications to control, automate and
document the entire semiconductor manufacturing process—from front end wafer fabrication to
assembly, test, and packaging on the back end.
Insights: And what value does—or can—a CIM solution provide?
Bing: When properly implemented, a turnkey CIM system can help manufacturers achieve rapid system deployment and faster productivity gains, which is especially important not only for those companies with existing factories that are competing harder on cost, quality, and cycle time, but also for new companies with limited prior experience building their first fabs. For new fabs time is incredibly valuable; deploying a fully integrated CIM is an avenue for helping such fabs achieve first silicon and volume production targets earlier, to meet technology and commercial requirements (see Bringing production reality closer to target).
Insights: In your view, apart from deployment and speed, what other challenges do semiconductor fabs often have to address when adopting a CIM?
Bing: For today’s semi fabs, we typically see manufacturing automation spread across four main areas, including manufacturing execution, process quality control, productivity efficiency, and supply chain integration. Connecting and integrating all these manufacturing domains across the many areas of a fab—and doing it in a cohesive manner—is one of the most time-consuming aspects of deployment. It can take anywhere from 6 to 12 months because every fab and its products are different, which requires significant customization from one factory to another. A considerable amount of time also must be spent validating the extremely complex manufacturing processes needed for a fab’s products.
Another big challenge semi fabs face with implementing and operating a CIM relates to data consumption. Semiconductor automation systems rely on massive amounts of data integrated from different CIM components—data related to orders, products, process steps, equipment sensors, and operators to drive the business decision making process. This data typically resides in disparate CIM applications with their own integration methods. In some cases, data does not exist, is incomplete, or is manually maintained on an operator’s laptop.
Insights: What is Applied Materials doing to address this gap?
Bing: We’ve developed our SmartFactory CIM solution—a one-stop, turnkey, fully automated solution that integrates Applied Materials automation products across four essential factory domains, including manufacturing execution, process quality, factory productivity, and supply chain. The underlying systems for each of these domains are connected through a message bus (see Figure 1). This out-of-box integration provides synchronized real-time communication to enable seamless decision-making logic flow that controls the complex manufacturing operations in a fab. The off-the-shelf capabilities make it possible to ramp up a new semiconductor factory in less than 6 months.
Insights: In your view, what are the key performance indicators addressed by your CIM solution? Or those key areas of the solution worth highlighting?
Bing:
I’d say accelerated time to market, reduced cycle time and better factory monitoring. More specifically, I’d say five key areas are worth noting here:
Full-automation of manufacturing operations
SmartFactory MES 300Works® Full-Auto offers an MES framework and solution for integrating factory operations, such as material control, factory events, planning and scheduling, and equipment maintenance management and all in full automation mode.
Process quality and yield
Our Applied E3® process control framework provides industry leading applications for fault detection, run-to-run control, SPC, equipment automation, recipe management, yield management, and defect management, all of which are used on various manufacturing processes across multiple fabs to generate process quality results and maximize yield.
Factory productivity
Our SmartFactory APF productivity framework includes scheduling, dispatching and reporting, simulation and prediction, which are integrated with enterprise planning, equipment automation, maintenance management, and advanced process control to maximize equipment uptime for productivity gains. Full automation capability in the productivity domain reduces white space and wasted tool time to maximize factory output.
Time to market and cycle time
Our SmartFactory workflow engine, empowered by production simulation, provides intelligence in workload prediction and reduces material wait time, resulting in shorter cycle times and overall time to market.
Factory monitoring
Worth mentioning here is our SmartFactory monitor solution, which patrols all CIM solution components, as well as enhances and protects factory operations. Its automated installers and easy-to-use features enable customers with lower cost of support and ownership.
Insights: Finally, what would you say is unique about Applied’s CIM offering?
Bing: Definitely experience. What I mean is that our SmartFactory CIM solution has been built with the best industrial expertise and knowledge in the industry. As the largest deployed CIM solution in the global semiconductor industry, it has been “hardened” (or developed over time) with each successive factory install. I think the key differentiators of our solution include:
Largest deployed CIM solution
Applied Materials is the leading semiconductor industry automation solution provider, with a team of nearly 1000 experts and three decades of experience automating semiconductor fabs.
Low or no customization requirements for integration
Most manufacturing operation management vendors own only a subset of capabilities in semi factory full auto needs, which requires significant customization to integrate various vendor products to cover full factory needs. In contrast, our SmartFactory CIM solution includes a comprehensive suite of SmartFactory solutions that are pre-integrated to cover semi factory full auto needs with low or no customization requirements.
Off-the-shelf capabilities
Applied SmartFactory EngineeredWorks® provides the pre-composed dispatching rules, MES automation rules, and R2R controllers that support over 90% of factory full auto operation scenarios. These off-the-shelf capabilities enable fast deployment for new fab startups and speed to market.
Powerful self-service platforms
The APF platform allows factory industrial engineers or planners to program customized dispatching rules for specific dispatching situations without having to involve IT resources. Similarly, our Applied E3 platform enables factory process engineers to create run-to-run process controllers to tune their specific process parameters. These platforms empower users to control fab behavior.
Conclusion
Applied’s fully integrated SmartFactory CIM solution includes a wide breadth of mature capabilities, spanning manufacturing execution, process quality, factory productivity, and supply chain management. The semiconductor industry is using this automation suite to attain predictable yield and output results.
Ready to contact us to learn more about our SmartFactory CIM or other solutions?