Introduction to durables management (DM)
In semiconductor manufacturing, durables are critical assets such as a reticle, carrier, probe card, pump or valve, chambers, fixtures, robots, and other equipment used in the manufacturing process. Durables can be considered mobile extensions of the manufacturing tool. Durables management, then, is the comprehensive management of these assets. It involves tracking, monitoring, and optimizing their usage, maintenance, and lifecycle to ensure smooth operations and maximize productivity.
Durables management is extremely important to semiconductor manufacturing for the following reasons:
Cost efficiency: Semiconductor manufacturing involves high-value equipment and efficient management of these assets helps reduce costs associated with maintenance, repairs, and replacements. By tracking the usage and condition of durables, companies can identify and address issues promptly, preventing costly breakdowns or unnecessary inventory.
Operational efficiency: Optimal utilization of durables is crucial for maintaining consistent production schedules. Effective durables management ensures that equipment is available when needed, minimizing production delays and maximizing throughput.
Process optimization: By monitoring the performance and health of durables, semiconductor manufacturers can gather valuable data and insights. This data can be used to identify patterns, optimize equipment settings, and improve overall process efficiency. Durables management software can provide real-time analytics and actionable insights to drive continuous improvement initiatives.
Maintenance planning: Durables management enables proactive maintenance planning by tracking asset usage and predicting maintenance needs. Predictive maintenance strategies can utilize the lifecycle data from the durables management system.
Quality control: Durables management helps ensure consistent product quality by monitoring and controlling the performance of critical assets. By tracking equipment performance metrics, semiconductor manufacturers can identify deviations and take corrective actions to maintain product quality and yield.
SmartFactory Durables Management offers several benefits that directly address the challenges faced in semiconductor manufacturing through the triad of traceability, state model, and integration, as shown in Figure 1. It is an automated durables management system that properly manages the state and location of durables throughout their life cycle, which is essential for achieving optimal product quality, cycle times, and tool utilization rates. Combining these with SmartFactory Real Time Dispatching (RTD) creates an unparalleled powerhouse for running assets at peak efficiency.
Assembly Test and Packing (ATP) burn-In use case example
Over the course of the last three years, Automation Products Group worked to develop, update, and modify durables management capabilities that can be universally used irrespective of a customer’s MES. The fundamental difference in the back end is that many activities are often manual. The first project of interest was a back-end burn-in facility. This facility is responsible for testing devices that have been packaged for delivery to customers. The devices are loaded on burn-in boards, sometimes referred to as BIBs (see Figure 2). These boards will circulate between loading equipment known as Burn-in Loading Units (BLUs) and then sent to burn-in ovens where the BIBs and devices are heated while parametric tests are run on them.
The industry has been looking for a way to manage these assets to gain reliable testing of devices as well as manage the expense of maintaining these durables in the facility. Manual handling of such activities would be extremely challenging. It is fair to say that, from the human perspective, it can be a daunting task to track that many durables. For example, it is estimated that a facility could contain as many as >20,000 or more durables of one type alone. The BIBs are populated with sockets and a single BIB can contain as many as 150 sockets. If sockets are defined as a durable as well, we now could be looking at a much greater number of durables to manage. It’s not simply a question of health management, but also of logistics. A burn-in facility has the fiduciary responsibility to test devices and isolate those that fail for one reason or another, as well as assure that the failure is coming from the device and not the BIBs and/or sockets. A prerequisite in such a facility is to be able to manage a remeasurement scenario in the event of a failed device. These activities are greatly facilitated by having the ability to track and trace the location and performance of the boards and the sockets upon them.
Optimizing remeasurement use case
Asset performance use case
Integration
More automation is needed to make durables management less daunting for the humans responsible for it. This automation can only be made possible if the durables have an application in which equipment integration can be connected. There must also be a provision for manual interfaces, as many of these facilities still rely on operators to load and unload equipment. This means that the ability to define relationships between boards and equipment and people is an essential part of a durables management system. It is also important to be able to define criteria that are tracked for the purposes of evaluating the health of durables. Last but not least, it is essential to establish a relationship between one durable and another in instances where they may contain each other or affect each other in some way. An example might be a container that is considered a durable which contains another durable, such as a cassette and reticle in a front end fab, or a BIB and a socket in a back end fab. These durables are expected to move throughout the day, often into equipment or out for repair and, in many cases, even outside the facility. To that end, a modern durable management system needs to have the ability to define and manage relationships both inside and outside the facility.
All durables must be able to maintain a state model that defines a business process of interest for the given durable. This business process will include simple elements such as counters and custom fields as well as parametric results from inspection tools or other calibration equipment. All these elements must be able to affect the behavior of the state model.
User experience/user interface elements of success
A well-thought-out product will make provisions for automated data entry generally supported by an application programming interface (API). Equally important is the human interface which may allow entry via a keyboard, mouse, barcode gun, tablet, or phone. The key component to a successful deployment of durables management is making it as unobtrusive as possible to the end user while allowing a growth path toward increased automation. This means that, as tasks are automated, updates to the automation behavior are easily accommodated. Equally important is that there is a visualization element for the user community.
SmartFactory Durables Management adopted several guiding principles to that end:
- Navigation and intuitive design are an essential part of a successful adoption of a durables management system.
- All the interfaces supporting this application will need to make use of lean efficiency principles.
- It is essential that such an interface be well designed to facilitate a natural progression of thought from the user and an ability to handle single or batch actions in a simple and concise manner.
- It is best if the interface supports these actions as if they were an extension of the human being’s behavior.
- All these various elements must allow inputs to drive the behavior of the state model.
- The equipment interface or RFID tags may also play a role in traceability of durables in the facility.
- A well-thought-out user interface allows the user to visualize at a macro level the durable of interest such as a bib. From that visualization, the ability to drill down to an individual socket is also a requirement. (See figure 3.)
Conclusion
About the Authors
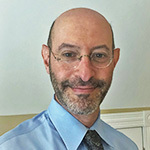
Selim Nahas is responsible for the Process Quality Group. Selim has 29 years of experience in semiconductor factory automation systems. He is a technical marketing specialist developing new solutions and methods of improving quality in semiconductor manufacturing. With a portfolio of technologies and developers with diverse specialties, the Process Quality Group develops and deploys Statistical Process Control systems for both Inline and Electrical Test as well as Fault Detection, Run to Run control and Recipe Management. This entire portfolio of capabilities is tightly coupled with one of the most advanced Knowledge Management Systems currently available in industry.
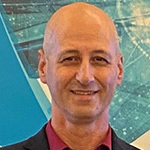
Prior to joining Applied Materials Automation Products Group in 2020, Yoram was a Global Marketing Manager at BASF Human Nutrition business division and before, an Innovation Manager for the Biosciences R&D Division at BASF. Yoram earned his PhD in Animal Sciences from the Hebrew University of Jerusalem and specialized in Biotechnology throughout his career.