Understanding Supplier Quality Management needs
Maintaining high-quality standards is paramount for any manufacturer. Supplier Quality Management (SQM) plays a critical role in ensuring that the materials, components, and services procured from suppliers meet stringent quality requirements. An ideal system will:
- Provide a single source of truth for all quality related information
- Facilitate better communication and collaboration between the manufacturer and the supplier
- Offer real-time monitoring of supplier performance through key performance indicators (KPIs) to quickly identify and address quality issues and ensure continuous compliance
- Automate the audit and assessment process, making it easier to conduct regular quality audits
- Enable leveraging of data analytics to support continuous improvement initiatives and help identify trends and areas for improvement
Improving supplier quality prevents incoming quality control inspection and improves supply resiliency. Incoming quality control (IQC) in semiconductor manufacturing refers to the process of inspecting and verifying the quality of raw materials and components before they enter the production line. This is a critical step to ensure that only materials meeting the required standards are used in the manufacturing process, thereby preventing defects and ensuring high product quality. Key aspects of IQC are illustrated in Figure 1.
Use case: workflow and state model part ordering management
Incoming inspection value vs. added costs
The current incoming practices of remeasuring materials when they are received provide little value and reassurance to your manufacturing quality. In fact, this process requires increased inventory stock and inhibits Just in Time (JIT) strategies. Among the costs within incoming programs that can be reduced are:
- Facility inspection floor space
- Inspection equipment and associated maintenance
- Material stored pending inspection
- Elimination of non-conformance Returned Merchandised Authorization (RMA)
- Resources required to support incoming inspection
Supplier Quality Management for your incoming program automatically verifies material quality and adds stringent controls essential to product manufacturing genealogy. Because your suppliers proactively receive nonconformance notifications, products can be held at shipment, rather than requiring your incoming department to complete the same validation process. This initial review and validation process creates the ability to address nonconformance sooner and builds supplier confidence.
Conclusion
Effective Supplier Quality Management is essential to maintain high quality standards and ensure the reliability of their products. It allows your incoming inspection to focus on verifying the supplier’s quality controls system, improving the time from when material is received to manufacturing. It also provides greater visibility into material health. By implementing advanced supplier quality software that meets the typical requirements, companies can achieve supply chain excellence.
About the Authors
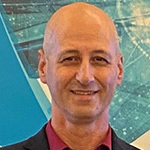
Prior to joining Applied Materials Automation Products Group in 2020, Yoram was a Global Marketing Manager at BASF Human Nutrition business division and before, an Innovation Manager for the Biosciences R&D Division at BASF. Yoram earned his PhD in Animal Sciences from the Hebrew University of Jerusalem and specialized in Biotechnology throughout his career.
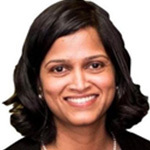
Vishali has been working in the semiconductor industry for more than 15 years. Prior to joining Applied Materials, she worked at Micron Technology, first as a process engineer and then as a senior quality engineer. She has been with Applied for seven years, having joined the company as a quality solutions architect. Vishali is currently a Global Product Manager overseeing SmartFactory SPC3D, an advanced process control (APC) engine that runs statistics to determine if processes are within spec to improve product yield. Vishali has an MS in mechanical engineering from Oklahoma State University, and a bachelor’s in mechanical engineering from Osmania University, in Hyderabad, Telangana, India.