This 3-part blog series was inspired by a live presentation delivered at SEMICON India on September 11, 2024
Live Presentation
“Evolution of Smart Manufacturing: Lessons for India’s Leap Ahead to Advanced Automation.”
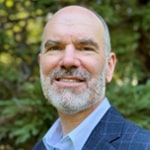
Scott Rothenberg
Key elements of smart manufacturing
Key Element 1: Material Transport
Key Element 2: Equipment Control Software
The software responsible for operating and controlling the equipment is another crucial element of a smart factory. It goes beyond automating basic start and end operations. Modern engineering software solutions excel at managing numerous process recipes, collecting and analyzing data from countless real-time sensors, and making dynamic adjustments to recipes to optimize product quality.
Key Element 3: Exception Handling Capability
Key Element 4: Learning Factory Automation Solution
Roadmap to leap ahead
- Full Auto Manufacturing: It is no longer a luxury, but a requirement. Meeting today’s customer requirements for quality and supply chain dependability necessitates factories running with full automation.
- Integrated Automation Solution: Avoid the pitfalls of piecing together automation components from multiple suppliers. Opt for a proven, comprehensive solution to minimize costs and deployment efforts.
- Scalable Solutions: Choose software that can adapt and grow with your factory for the long term. Look for solutions that support future advanced computing technologies.
- Gradual Automation Journey: Start with out-of-the-box capabilities and gradually customize and enhance the system as your experience, needs, and factory evolve. Move at a pace that suits your requirements.
- Trusted Partner: Select an experienced partner who understands your automation needs and has a proven track record. Let them handle software deployment, technical support, and enhancements while you focus on other aspects of building and running your factory.
Conclusion
These are exciting times for the semiconductor industry as we embark together on India’s Semiconductor initiative. India has a tremendous advantage in being a new entrant to this market, as it can benefit from all the learnings and costly investments of its peers. But perhaps the area where it has the most advantage comes from the ability to leapfrog manufacturing productivity and quality achievements by adopting state of the art factory automation.
For more information, check out our SmartFactory Semiconductor Blogs and Semiconductor LinkedIn posts.