This 3-part blog series was inspired by a live presentation delivered at SEMICON India on September 11, 2024
Live Presentation
“Evolution of Smart Manufacturing: Lessons for India’s Leap Ahead to Advanced Automation.”
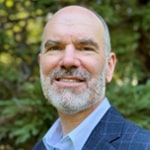
Scott Rothenberg
What’s Inside
In the first blog of this series, we looked at the origins of manufacturing and what it means to make it “smart.” In this blog, we’ll dig deeper into “leapfrogging” and the semiconductor industry’s role in pioneering the technology that makes it possible.
“Leapfrogging”
The concept of “leapfrogging technologies” can be defined as “bypassing the traditional evolutionary phases of research, development, investment (and failure).” Does this leapfrogging really happen? Yes, absolutely. We see this across multiple industries, including telecommunications, banking, agriculture, power generation, computers and now, semiconductor manufacturing. As new technologies are developed, those who wait to implement can skip over costly investment and infrastructure development and move directly to low cost, rapid deployment and adoption. For example, in 1990, about 5% of households in India had a phone line. Today, there are more than 1 billion smartphone users in India, representing quite a leap.
Semiconductor pioneers
The semiconductor industry spearheaded the technologies that led to Industry 4.0 and the age of Smart Manufacturing—and make it possible for countries like India to leapfrog technology today. The early pioneers in the industry, who we’ll call innovators, took the same approach with factory automation software as they did with process equipment; they built their own. There was no ecosystem of commercial software suppliers to support the industry. Indeed, there was hardly any industry at the time, and each company solved what seemed to be its own unique manufacturing problems with its own unique software solutions. This software was rudimentary in nature and, while functional, was never architected or engineered to provide decades of mission-critical use. It was generally single-purpose, not scalable and often written and supported by a few talented individuals who were loath to allow anyone else to see the code, much less edit it.
In the 1980s and ’90s, new entrants to the industry didn’t have the technical expertise, money, or interest to develop their own software. As a result, an industry began to sprout that provided specialized products that would address one of several aspects of manufacturing automation. These included Manufacturing Execution Systems (MES) to track the flow of material; Statistical Process Control (SPC) to help improve quality; Material Control Systems (MCS) to control material handling hardware; and Real Time Scheduling to prioritize lots for processing.
Early adopters of these products needed significant expertise to turn what was essentially a set of toolkits (each of which could theoretically “do anything” but that in practice “did nothing” without a lot of expert engineering) into a solution. There were still tools and systems that weren’t available commercially, or were deemed too immature, or lacking in features. These software components still needed to be written and supported by the factory’s own engineers.
Where we are today
Today, it’s rare to find anybody building a new factory who will follow that “Do it Yourself” approach to factory automation software. While there are still companies that created their own home-grown systems with a combination of commercial and internal software, deployed and supported by large, experienced IT teams, they too are increasingly abandoning this approach.
The smart manufacturing approach is revolutionizing – and democratizing – semiconductor manufacturing in both wafer fabrication and packaging. Smart manufacturing entails turn-key, fully integrated, fully featured software solutions that – out of the box – can run a manual pilot line, all the way to a full-auto, lights out, high volume manufacturing facility. Not only does today’s software have more functionality, but it is also more stable, supportable and scalable. It’s simply better.
Up Next
In the next blog in the “Evolution of Smart Manufacturing” 3-part series, we’ll dig deeper into the elements of a smart manufacturing solution.
For more information, check out our SmartFactory Semiconductor Blogs and Semiconductor LinkedIn posts.